Interweaving between data and material, programming and construction, the digital fabrication techniques synthesize the design and construction stage process, which empowered designers to be involved more in structural work. More importantly, it enables and energies the architectural structure to be a part of the design. Therefore, plus its significant potential in the efficiency of production and human-power saving, will this technology — digital fabrication — be able to further enhance architecture performance in reliability, sustainability, and humanistic care to carry out heavier social responsibilities? Through a series of case studies on various assembly typologies, this research aims to develop a method of joining applicable to a rapid assembly system of various scope to serve as a large temporary post-catastrophe architecture and reusable in other ranges after being dismantled. In such a way that the assembly system potentially is adaptable to the broader application.
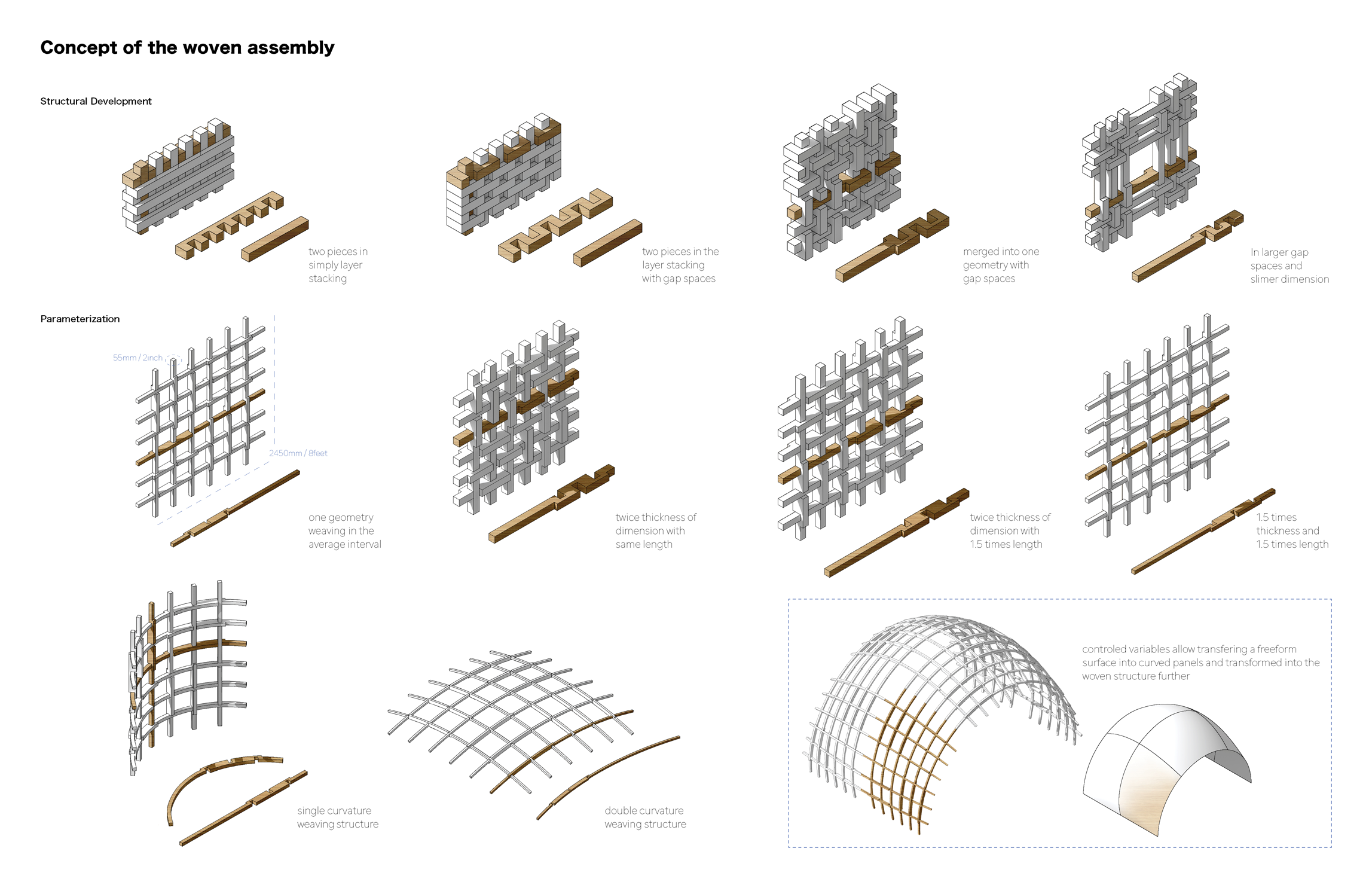
Weaving is acknowledged as one of the oldest surviving crafts in the world. It has two predominant characters: self-tight and a simple repeat method, making it the best candidate for applying to digital fabrication – achieving a simple and efficient assembly method by putting effort into a complicated geometric form-finding. Beginning with mimic the movement of “warp and weft” — taking thread and loop it back and forth over a loom to make the warp, and then weave back and forth through the warp to make the weft, the original wall-shape module created. Finally, by controlling with two variables, the thickness of components and the length, a customizable panel-based module could be produced to meet any circumstances or environment request in terms of scale and dimensions. In other words, as long as having a free form surface, dividing it into multiple suitable sizes and calculating curves degree on the surface, a self-tight woven structure system is able to be automatically generated.
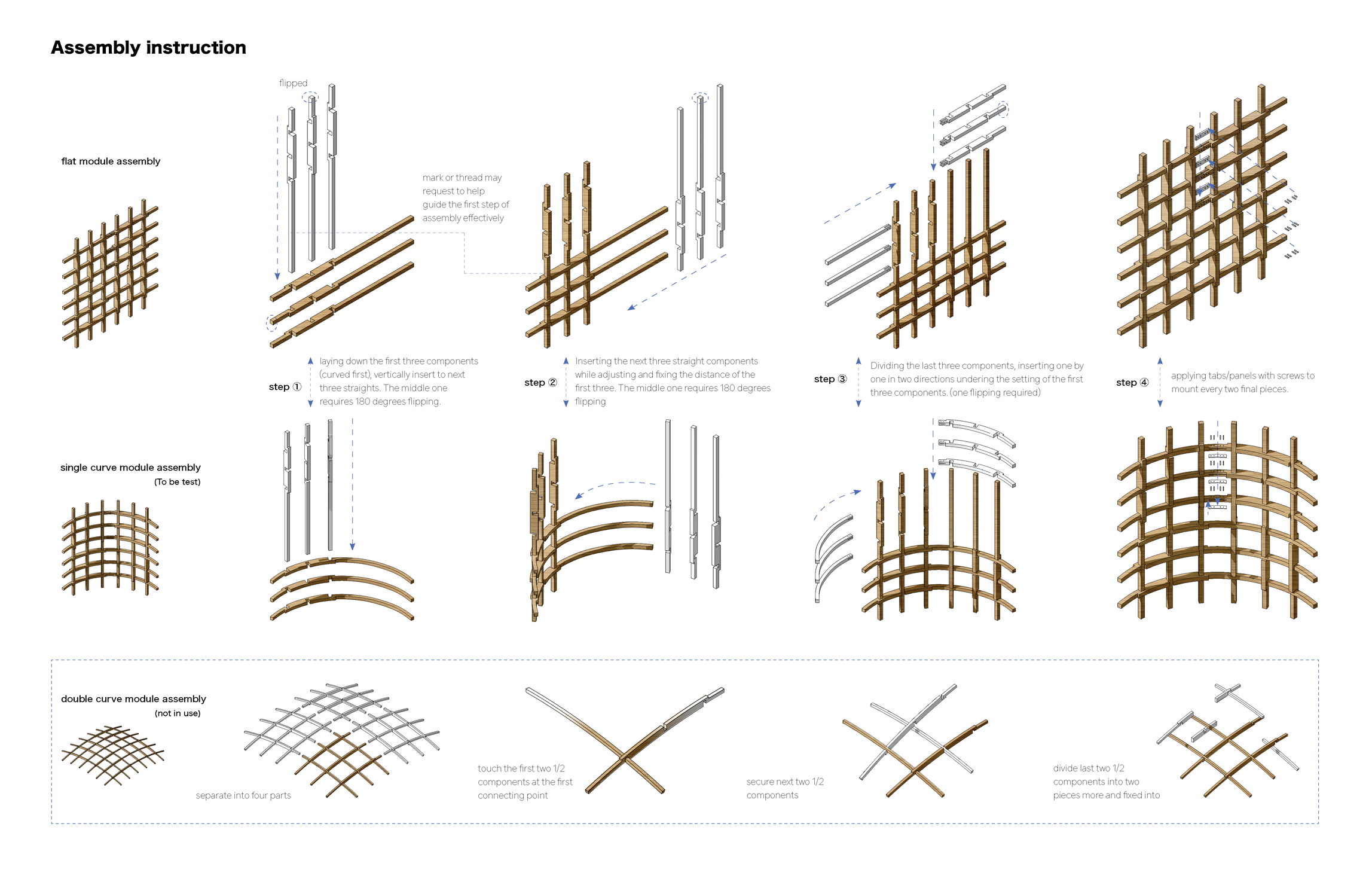
How efficient the assembly is one of the key pursuits of this system. By giving a visualized guide or short training, this assembly system expects to make even non-professional able to help to finish part of the assembly work so that has the potential to deal with more circumstance.
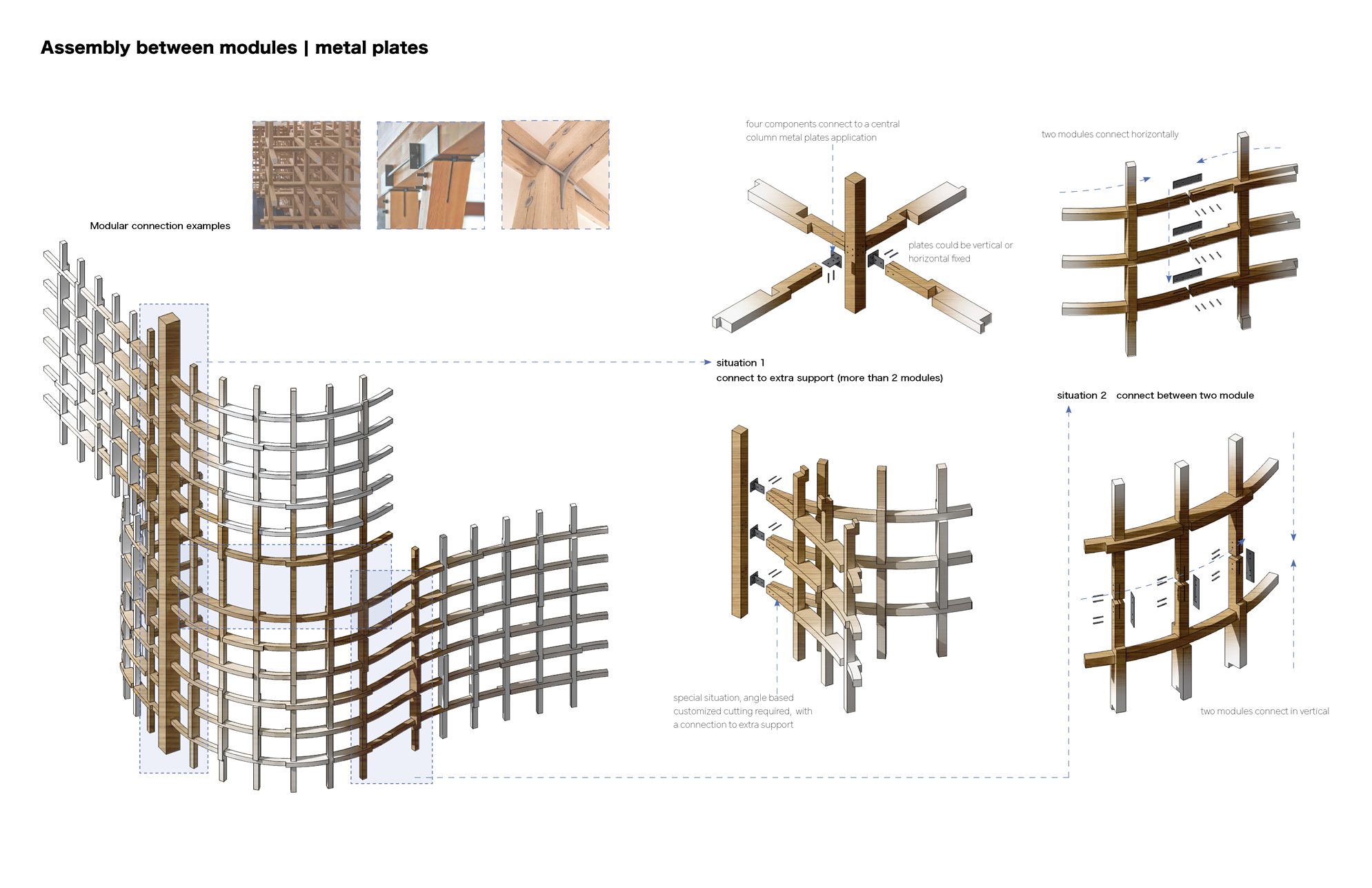
There are two situations that might meet when a connection between each module required. The first proposal is to directly connect each other referring to Kanko Kuma’s GC museum project, cutting two edges of connecting side, inserting the tab and secured by a threshold. For the situation that requires more than two components or applies for heavy use, connection to an extra support column with mechanical metal plates joining is suggestive.
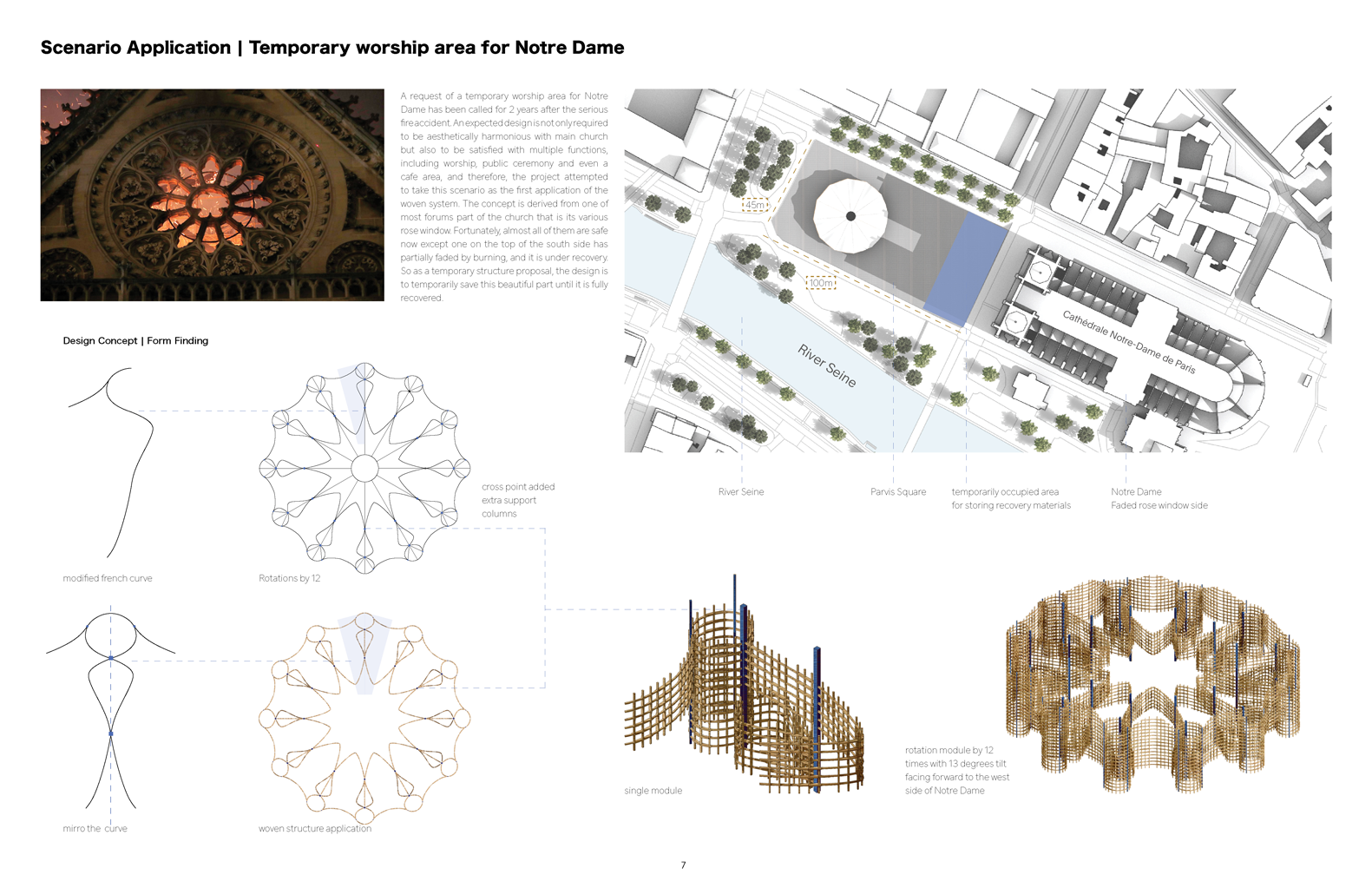
Scenario application – temporary worship area for Notre Dame
A request for a temporary worship area for Notre Dame has been called for 2 years after the serious fire accident. Although many architects have proposed various proposals, none of has been approved to practice as designing is not only required to be aesthetically harmonious with the main church (site is located on the parvis square near the west side of the church, which was the main entrance for tourist) but also to be satisfied with multiple functions, including worship, public ceremony and even a cafe area, and therefore, the project attempted to take this scenario as attempt application of the woven system. The concept is derived from one of the most famous parts of the church that is its various rose window. Fortunately, almost all of them are safe now, except one on the top of the Southside has partially faded by burning, and it is under-recovery. So as a temporary structure proposal, the design temporarily saves this beautiful part until it is fully recovered.
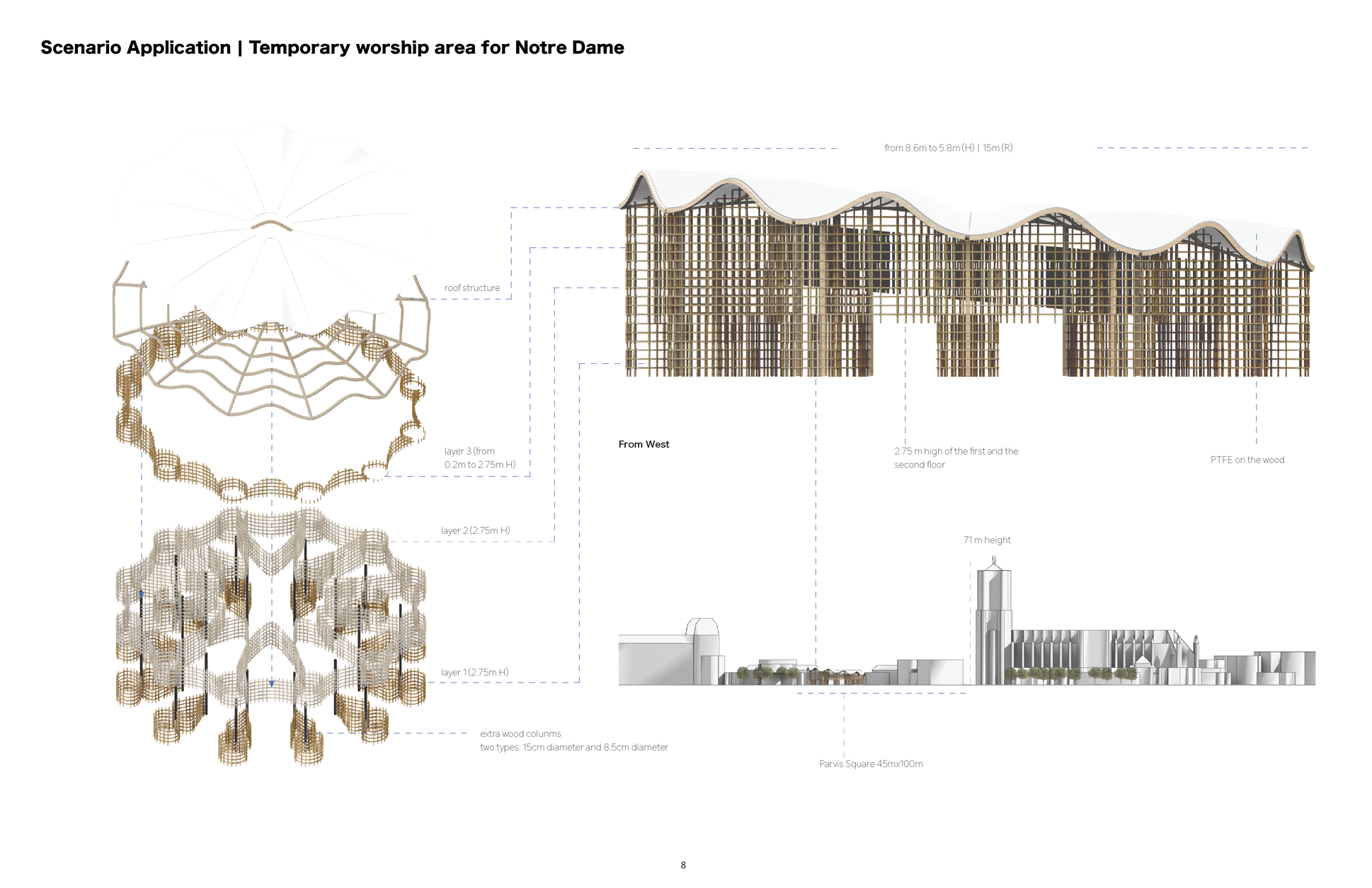
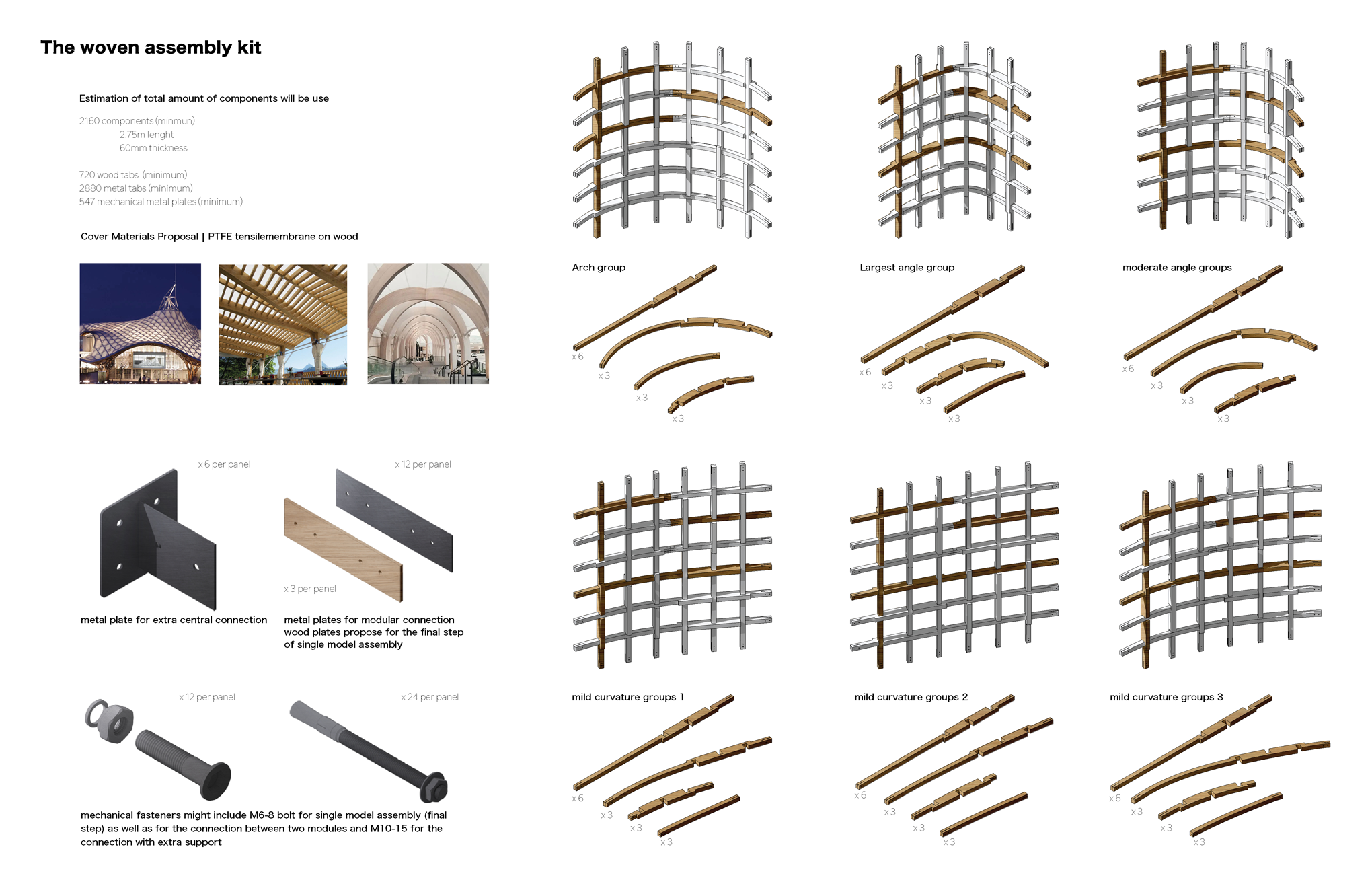
A modified traditional french curve is the base of the design concept. By mirroring this curve and rotation 12 times, the design aims to create an adaptive version of the original shape and design of the faded rose window. Totally, there will be at least 2590 components, 720 wood tabs,2880 metal tabs and 547 mechanical metal plates estimated to be in use to complete this 3 layers structure. With a slight tilt degree towards the west side of the church (main entrance), the highest part would be 8.6m and 5.6m on the lowest side. 12 opening entrances are in the same dimension with 2.75m high. This proposal would totally occupy a 706.8m area.
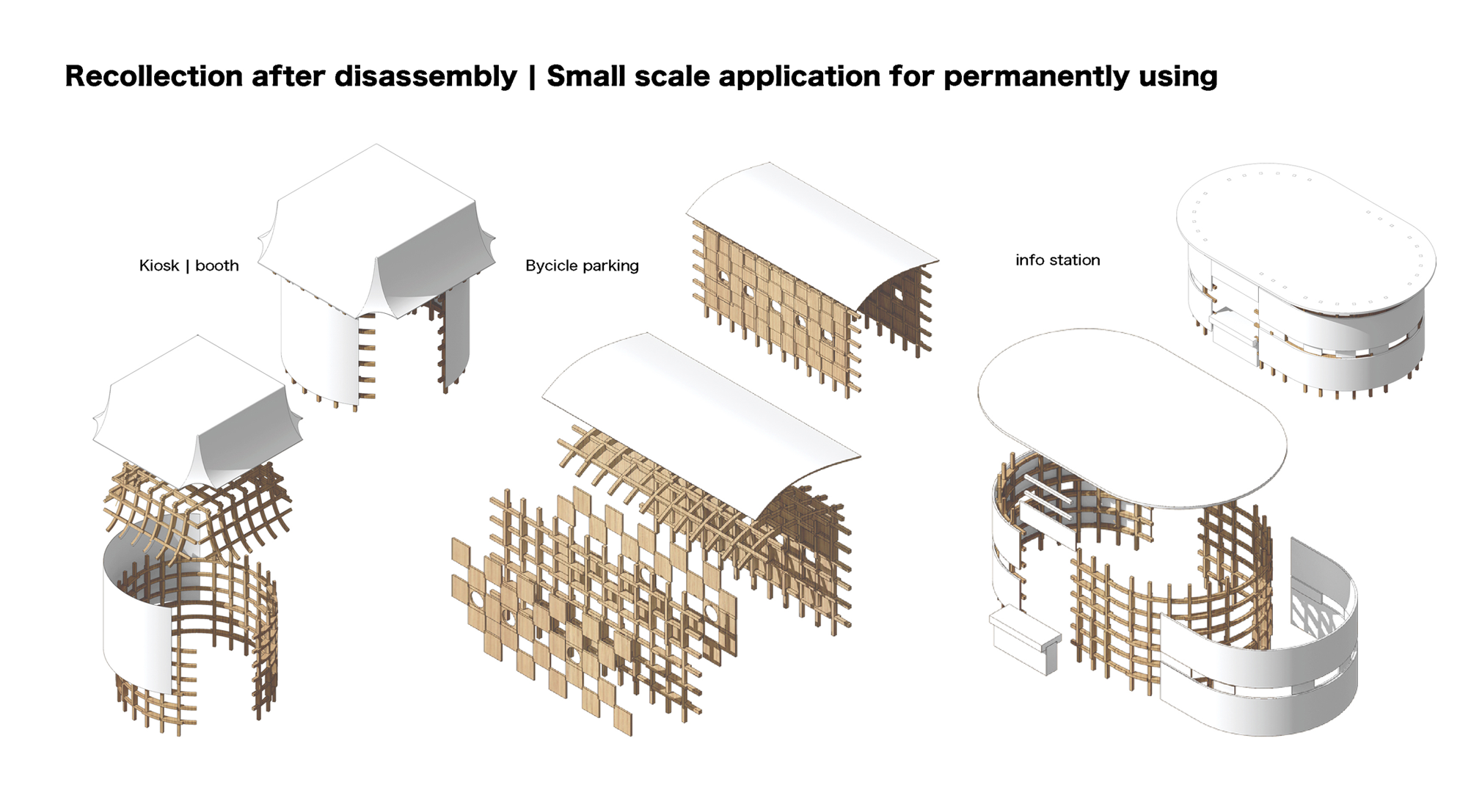
How much a temporary structure should cost is always the key debating point of the design and fabrication. Over 2000 components cut by CNC for a structure with only 6 years long life is not a small portion, not to mention the metal and wood joining. Moreover, the uncountable consumption on the time of fabrication and human power. Indeed, 6 years for a building is ignorable shortness. However, for a span of memory of human life is long enough. What is more, for a post-catastrophe design, should the symbolic function of healing be valued as same as its practical function of space or even more? So instead of compromising the cost, giving this design a second life after dismantled is my proposal for a solution to this debate. Since the system itself is module-based, in other words, all of these panels can be re-arranged and re-assembly in different ways. Therefore, a series of reuse strategies such as a kiosk, info station or bicycle parking area is proposed as a permanent structure. Taking advantage of its strip-shape, which might be possible to transport to more places, the woven system is expected to continue its mission living in any other place on this world and bearing its short experience as a temporary worship place.
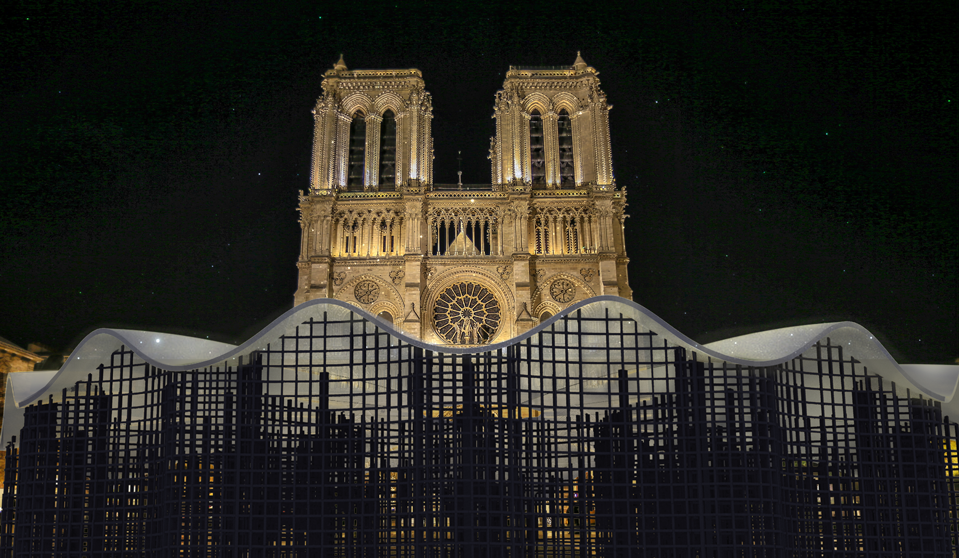
As an architectural proposal for a post-catastrophe project, I hope that the assembly proposal is not only to create space but also to let the meaning of weaving can “tie up” everyone together.